

The full pressure pulse develops only when the reflected pressure wave returns to find a closed valve. The time period (t) is the time the pressure wave takes to spread along the upstream line and reflect back to the valve. If the water line in the example above is 100 m long, then: The full force of the pulse develops only when the change in velocity is sudden, specifically when ∆u occurs within a given time period (t), as determined by the following equation (in which L is the length of the liquid line): In practice, the pulse pressure may not be as high as that calculated by the Joukowski’s Law equation. And the pressure pulse will be even higher if the liquid sampling system flows at a higher velocity than 1 m/s. This extra pressure spike may not be tolerable for this particular system. That’s 14 bar of additional pressure that you have likely not planned for in your sampling system. Therefore, when the operation of a valve suddenly stops a water flow with a velocity of 1 m/s, the calculated pressure pulse is: For example, the speed of sound in water at 20☌ is about 1400 m/s. The parameter c is the speed of sound in the liquid under actual operating conditions. These parameters can be entered into an equation known as Joukowski’s Law, which estimates the magnitude of the water hammer pressure pulse (∆P) experienced in a line when the liquid velocity (u) suddenly changes by ∆u. You’ll need to know a few specific details, including the density (Ï) and velocity (u) of your sample fluid.
#Water hammer how to
But first, let’s review how to determine if water hammer may impact your sampling system. Without a means of escape, the pressure spike can be severe enough to damage components anywhere in the line.Ī variety of mitigation methods can help to avoid the sudden pressure spikes of water hammer. The resulting pressure wave travels upstream in the tube and, unfortunately, the pressure rises too quickly for a typical proportional relief valve to open and release it. This pressure surge originates in the compression of the liquid and from deformation of the tube walls. Therefore, the force required to decelerate the liquid creates a rapid increase in pressure. The liquid is heavy, and it’s travelling fast. When the operation of a valve suddenly interrupts the flow of a liquid, something has to absorb the momentum of that liquid and bring it to a standstill. In addition, we’ll review a few methods for mitigating the water hammer effect, including using needle valves for shutoff, diverting flow instead of shutting it down, and using pressure snubbers to protect gauges. Let’s take a closer look at why the phenomenon of water hammer occurs and how to estimate its effect in your sampling system. So they have trouble understanding where the extra pressure originates. They know the maximum process pressure won’t exceed the system’s design.
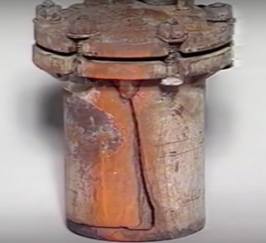
Yet operators often don’t realise what caused the damage. It can even burst lines or end connections if the pulse is too great. This pulse of additional pressure can be enough to damage every pressure gauge or flowmeter upstream of the closed valve. Water hammer strikes as a sudden pressure pulse that is in addition to the working pressure in a system. This occurs because a steam bubble is sometimes trapped in cold water and condenses very rapidly, accelerating and decelerating a column of water very rapidly.It’s known as water hammer, and it occurs when a valve abruptly closes and liquid flow is suddenly stopped. Filling or draining a pipe in which cold water replaces steam or steam replaces cold water very often leads to water hammers and damage to piping supports, valves, or the pipes themselves. Water hammer in steam systems is most likely to occur when a vapor bubble is trapped by cold water and condenses very rapidly. If two phases are present, the velocity of sound in the two phase mixture is greatly reduced so that excess pressure due to a water hammer in such a flow is rarely a problem. A useful rule of thumb for estimating water hammer pressure is, for each m/s of extinguished velocity, the pressure rise is 10 6 Pa. In a typical pipe, the elasticity of the walls, in effect, reduces the v s by about 10%. In which ρ is the density of the liquid, v s the velocity of a pressure wave (a sound wave) in the pipe and Δv is the extinguished velocity.
